Mise en place d'une ligne d'assemblage de compresseurs
*ENISE (École Nationale d'Ingénieur de Saint-Étienne) Promotion 2000/2005 3GM
Mots clefs : ENISE, SULLAIR, Compresseur, Assemblage, Organisation, Kanban, Flux tendu
Résumé :
Rapport de fin de période industrielle chez SULLAIR EUROPE (Montbrison) du 08/07/2002 au 23/01/2003
Remerciements
La première période industrielle d'un élève ingénieur est une étape importante de son cursus. Elle permet de mettre en relation les connaissances théoriques apprises en cours avec ses applications dans l'industrie, mais aussi de les compléter par d'autres, plus en rapport avec le monde du travail.
Elle permet aussi de découvrir le fonctionnement d'une entreprise et des différents services qui la compose.
C'est la raison pour laquelle je tiens à remercier toutes les personnes qui m'ont permis d'avancer dans mon projet, à savoir:
-
Monsieur Jean-Claude RONDEL, mon ingénieur tuteur durant tout le stage, pour avoir été présent afin de répondre à mes questions et pour m'avoir laissé une grande autonomie dans mon travail.
-
Monsieur Bruno DEPLAUDE, mon professeur de stage, pour m'avoir fait confiance et m'avoir aidé au long du stage.
-
Messieurs Bruno FILLEUX et Joël PALLAY du bureau des méthodes.
-
Messieurs Christian EPINAT et Henri LEFEBVRE du bureau d'étude.
-
Les deux équipes de monteurs de la ligne compresseur pour m'avoir donné de nombreux renseignements sur leur travail et sur la ligne actuelle.
Présentation de SULLAIR EUROPE
Historique
- 1900 :
-
Installation à Meudon (région parisienne) de la société des Forges et Ateliers de Meudon, elle est spécialisée dans la fabrication de gyroscopes de torpilles, mandrins pneumatiques et de pièces pour l’industrie automobile.
- 1939 :
-
Les Forges et ateliers de Meudon s’installent à Montbrison dans un ancien atelier textile, destiné à la fabrication d’outils pneumatiques (Industrie, B.T.P).
- 1953 :
-
La société MACO s’oriente vers la fabrication de compresseurs fixes industriels et de compresseurs mobiles pour le secteur du B.T.P.
- 1967 :
-
MACO quitte ses ateliers de Lyon pour s’installer dans une nouvelle usine, plus moderne à SAINT-PRIEST (à 10 Km de Lyon).
- 1970 :
-
Création de la société MACO-MEUDON, implantée à SAINT-PRIEST et à Montbrison, issue de la fusion de MACO et des Forges et Ateliers de Meudon
- 1979 :
-
MACO-MEUDON devient filiale à 100% du groupe allemand IBH.
- 1983 :
-
La maison-mère allemande dépose son bilan et entraîne avec elle toutes ses filiales dont MACO-MEUDON.
- 1984 :
-
L’ancien directeur général reprend la société et lui redonne un second souffle.
- 1988 :
-
Un partenariat est mis en place avec SULLAIR CORPORATION (Michigan City, États-Unis) pour la distribution d’outils pneumatiques aux couleurs SULLAIR aux États-Unis.
- 1990 :
-
MACO-MEUDON cède la totalité de ses parts à SUNSTRAND CORPORATION (groupe industriel ayant acquis SULLAIR CORPORATION en 1984).
- Avril 1993 :
-
MACO-MEUDON devient SULLAIR EUROPE S.A.
- Juillet 1993 :
-
Construction d’une nouvelle usine à Montbrison.
- 1997 :
-
Les difficultés financières de SULLAIR EUROPE contraignent SUNSTRAND CORPORATION à fermer l’unité de SAINT-PRIEST afin de rassembler la production des deux usines dans la seule unité de Montbrison.
- 1999 :
-
SUNSTRAND et HAMILTON TECHNOLOGY fusionnent pour devenir HAMILTON SUNSTRAND, un sous-groupe du géant américain UNITED TECHNOLOGIES (25 milliards de dollars et 150 000 employés)
Aujourd’hui, SULLAIR EUROPE est une société anonyme à responsabilité limitée au capital de 9 500 000 €.
L’effectif de l’entreprise est d’environ 140 personnes
Le chiffre d’affaires réalisé en 2002 est de 30,5 M€.
Le savoir-faire de l’entreprise est donc basé sur l’étude, la fabrication et la commercialisation:
-
de compresseurs d’air pour l’industrie et le B.T.P.
-
d'outillage pneumatique pour le B.T.P. (marteaux piqueurs, sablons, aiguilles vibrantes...)
L’entreprise est certifiée ISO 9001 (AFAQ N° 1992/520) et est en voie d'obtenir les certifications ISO 14001 pour l’environnement, et OSHAS 18001 pour la sécurité.
La production fonctionne en 2 équipes de 8 heures du lundi au vendredi.
L'organisation interne est décrite sur le schéma suivant :
Les produits
Outils pneumatiques
SULLAIR EUROPE fabrique une large gamme d'outils pneumatiques: Des piqueurs, des perforateurs ainsi que des brises béton. La fabrication de ces outils occupe le tiers de l'aire de l'atelier et reste le secteur principal de l'entreprise. Il y a deux familles de piqueurs: Les percutants (Brise bétons etc...) et les roto-percutants (Perforateurs...). Ils diffèrent tous par la taille ou les outils, mais ont tous le même principe de fonctionnement.
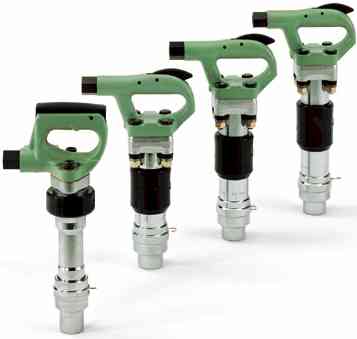
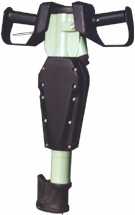
- 1 :
-
Lorsque la gâchette est appuyée, l'air alimente la distribution. Le piston est au point de frappe. La pastille est sur le siège de frappe. Le canal de relève se trouve en pression et l'échappement à l'air libre.
- 2 :
-
Le piston monte et commence à comprimer la chambre haute.
- 3 :
-
L'air de la relève est à l'air libre, la chambre haute est en pression et provoque le déclenchement de la pastille sur le siège de relève.
- 4 :
-
L'air provoque la descente du piston par l'intermédiaire du siège de frappe.
- 5 :
-
Le piston vient frapper sur l'outil. L'échappement se retrouve à l'air libre et le cycle recommence phase 1.
Bloc-vis
Il s’agit de la partie du compresseur destinée à comprimer le mélange air-huile. Les bloc-vis sont fabriqués à Montbrison et font l'objet de contrôles minutieux tout au long de leur fabrication. Ils sont assemblés sur les compresseurs SULLAIR, mais sont également vendus à d'autres fabricants de compresseurs tels que CHAMPION en Australie (Récemment acquis par la maison mère SULLAIR).
Il y a 2 modèles de bloc-vis:
- MM2 :
-
Pour les petits compresseurs de type S35 et S45.
- MM3 :
-
Pour les gros compresseurs S55, S65, S85 et S115.
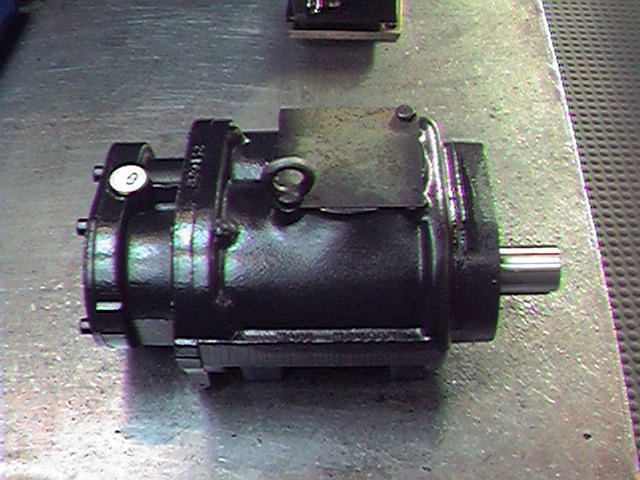
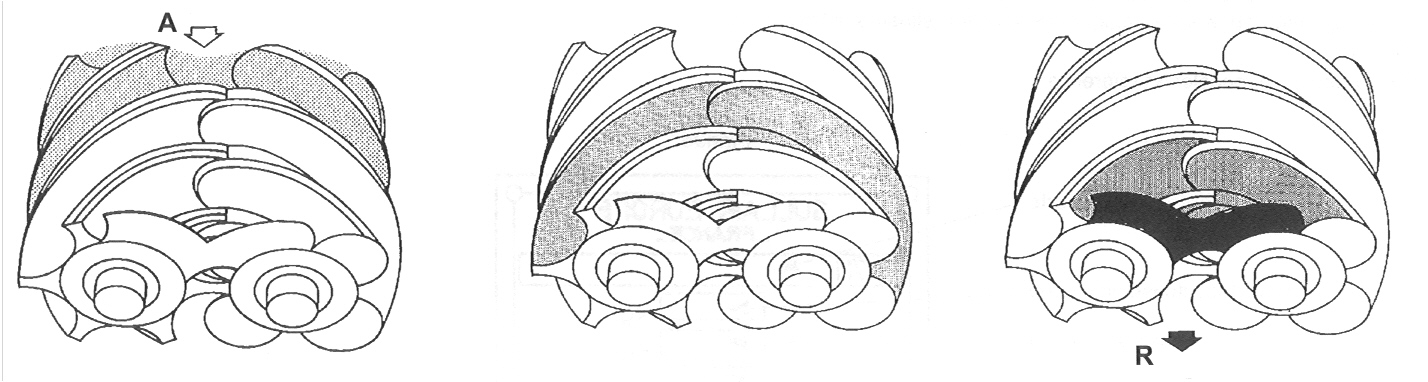
- ADMISSION :
-
En face de l'orifice d'admission A, l'écartement des lobes provoque une dépression permettant l'admission d'air dans le creux des vis.
- COMPRESSION :
-
L'engrènement des vis emprisonne l'air admis dont le volume diminue au fur et à mesure de la rotation.
- REFOULEMENT :
-
L'air progressivement comprimé arrive en face de l'orifice de refoulement R.
Compresseurs d'air
SULLAIR EUROPE fabrique des compresseurs portables de petite taille (Les gros compresseurs et centrales d'air sont fabriqués aux États-Unis et importés). Les petits compresseurs portables sont utilisés dans les chantiers en génie civil pour alimenter des outils pneumatiques (Piqueurs, brise béton...) mais aussi des sableuses destinées au ravalement des façades ou encore des sablons à crépir. Ils sont autonomes, entraînés par des moteurs diesel KUBOTA et délivrent une pression de 7 bars.
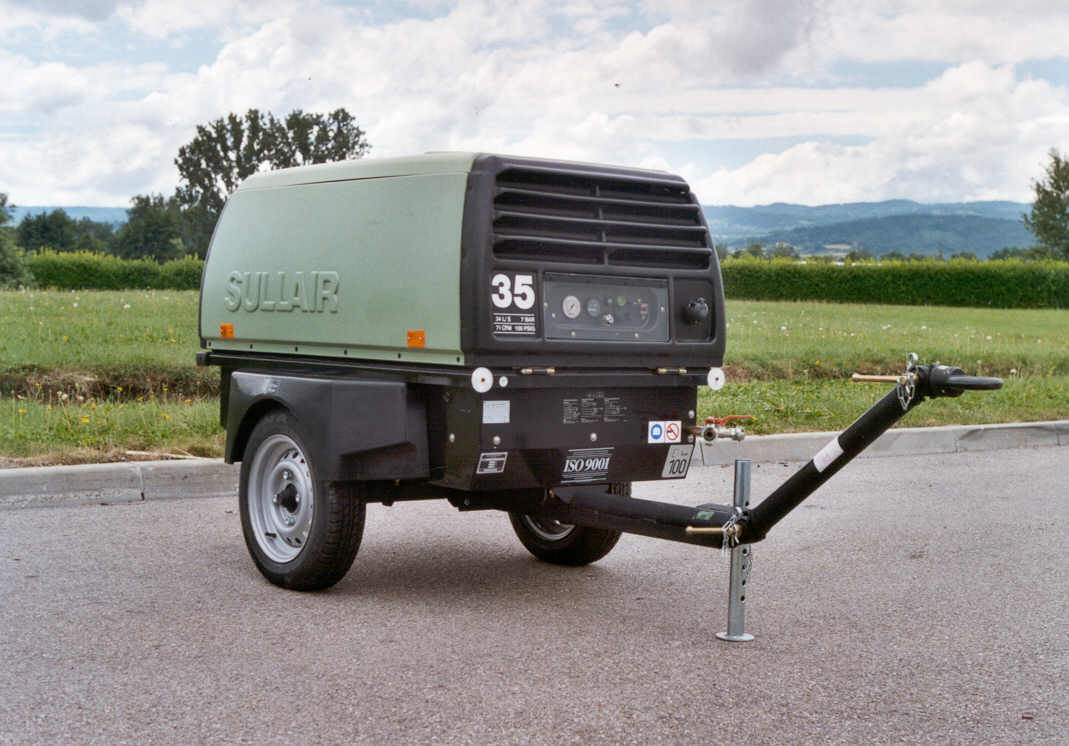
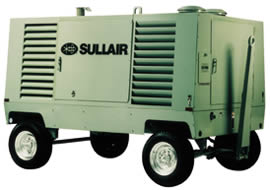
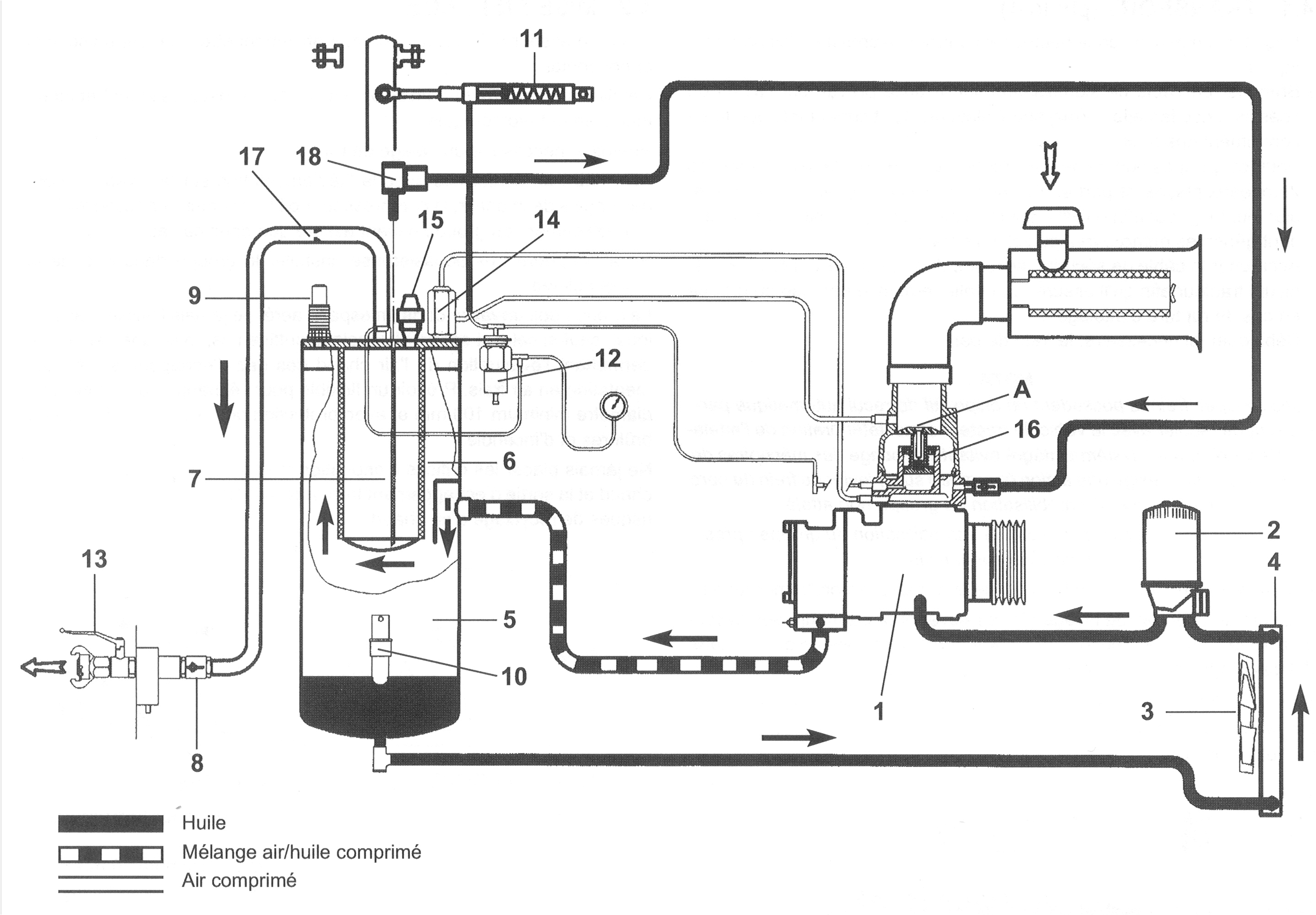
- BLOC VIS :
-
C'est un compresseur d'air à 1 étage. Il est lubrifié par l'huile qui y est injectée à chaque phase et mélangée à l'air par la rotation des vis.
L'huile à 3 rôles:
-
Lubrifiant entre les vis: Permet l'entraînement d'une vis par l'autre.
-
Refroidisseur: Elle limite l'élévation de la température due à la compression.
-
Joint d'étanchéité entre les vis et le corps et entre les vis elles-mêmes.
-
- 2 FILTRE A HUILE :
-
Il empêche les impuretés de pénétrer dans le bloc vis.
- 3 VENTILATEUR :
-
Il souffle l'air à travers le radiateur.
- 4 RADIATEUR
- 5 SÉPARATEUR :
-
C'est ici que l'air est séparé de l'huile par gravité dans un premier temps, puis par filtrage.
- 6 CARTOUCHE DE FILTRATION :
-
Elle retient l'huile encore présente dans l'air.
- 7 TUBE PLONGEUR :
-
Recueil l'huile au fond de la cartouche pour la renvoyer (Grâce à une différence de pression) vers le bloc-vis.
- 8 CLAPET ANTI RETOUR :
-
Empêche l'air comprimé du circuit de branchement de retourner dans le séparateur au moment de l'arrêt. C'est une sécurité en cas de coupure imprévue du compresseur. Il évite ainsi à certaines impuretés (Sable...) de rentrer dans le compresseur.
- 9 SOUPAPE DE SÉCURITÉ :
-
Elle s'ouvre lorsque la pression dans le séparateur dépasse 900kPa (9 Bar).
- 10 :
-
Retour de l'huile du séparateur dans le circuit.
- 11 VÉRIN DE COMMANDE DE VITESSE :
-
Directement lié à l'accélérateur du moteur, il commande la vitesse de celui-ci en fonction de la pression à l'intérieur du séparateur. Sous une pression de plus en plus forte, le vérin tend à ralentir le moteur.
- 12 RÉGULATEUR :
-
Il alimente les vérins 11 et 16.
- 13 ROBINET D'AIR
- 14 SOUPAPE DE MISE A VIDE
- 15 MANO-CONTACT :
-
Il empêche le démarrage du moteur tant que la mise à vide du séparateur n'est pas réalisée et empêche le déclenchement du démarreur quand le moteur tourne
- 16 VÉRIN DE CLAPET D'ADMISSION.
- 17 ORIFICE CALIBRE :
-
Il assure une pression minimum du séparateur de 3,5 Bar dans toutes les conditions. Cette pression est nécessaire à une bonne séparation et une bonne circulation de l'huile.
- 18 TAMIS :
-
Protège le circuit de retour et assure un débit correct.
- A CLAPET D'ASPIRATION
Le bloc-vis est entraîné par un moteur diesel KUBOTA par l'intermédiaire de 2 ou 3 courroies trapézoïdales.
La production
L'atelier se compose de plusieurs parties distinctes:
-
La fabrication et l'assemblage des outils pneumatiques
-
L'assemblage des compresseurs
-
La fabrication et l'assemblage des blocs vis
L’ensemble de la production est gérée en flux tendu tiré par la demande (DFT:Demand Flow Technology) et le pilotage s’effectue à l’aide d’une gestion par Kanban ("Étiquette" en japonais). Le flux est dit "tiré" car le démarrage de la production s’effectue à partir de la commande du client. Cela permet d'éviter un stock de produit inutile ainsi qu'une fabrication excessive de produits.
Une ligne en flux tendu se dimensionne en respectant les phases suivantes:
-
Définition des quantités à produire sur la ligne.
-
Dimensionnement de la ligne.
-
Dimensionnement des stocks à mettre sur la ligne.
-
Calcul des boucles Kanban.
-
-
Affectation des ressources de la ligne.
-
Définition de la séquence des événements.
-
Calcul du temps de cadencement ou takt time (Temps alloué pour la réalisation de chaque tâche).
-
Calcul des temps moyens et des taux d'occupation (Nombre de ressources nécessaires à la réalisation d'une tâche).
-
Affectation des ressources et équilibrage des opérations.
-
Calcul des temps de cycle.
-
-
-
Implantation de la ligne (Schéma).
L'affectation des ressources et le dimensionnement des stocks peuvent se faire indépendamment l'un de l'autre.
Le principe du Kanban (Signal sur une quantité) permet de réapprovisionner ce qui est consommé et permet de fabriquer ce qui est pris en commande.
À chaque lot de pièces usinées ou de composants, ainsi qu'à chaque produit fini correspond une carte Kanban.
Pour fonctionner correctement:
-
Cette gestion nécessite une très grande réactivité face à la demande, car le stock est le plus réduit possible.
-
Chaque produit doit être réapprovisionné au plus vite.
-
Les cartes Kanban ne doivent pas être perdues.
Présentation du stage
Découverte de l'entreprise
Lors de ma première semaine de stage, j'ai pris contact avec les différents services qui composent SULLAIR EUROPE (Méthodes, bureau d'étude, maintenance, production, comptabilité, etc...). J'ai alors pu connaître l'entreprise plus en détails sur son fonctionnement et sur les responsables des différents services avec lesquels j'allais travailler par la suite. Ces visites m'ont permis de comprendre le principe de la fabrication en flux tendu, la gestion de l'approvisionnement et le fonctionnement d'un compresseur d'air.
Mon stage portant sur la réorganisation de la ligne d'assemblage des compresseurs portables, j'ai travaillé sur la ligne pendant la deuxième semaine pour me rendre compte de la complexité et de la spécificité de chaque étape du montage.
Contexte du stage
En 1997, lors de la fermeture du site de SAINT-PRIEST, la ligne de montage des petits compresseurs fut ramenée à Montbrison. La ligne n'a alors subi qu'une seule modification en 5 ans. La production annuelle de 600 compresseurs en 1997 est passée à 1348 compresseurs en 2002, et la demande de compresseurs ne cesse d'augmenter avec les nouveaux marchés que SULLAIR a réussi à obtenir.
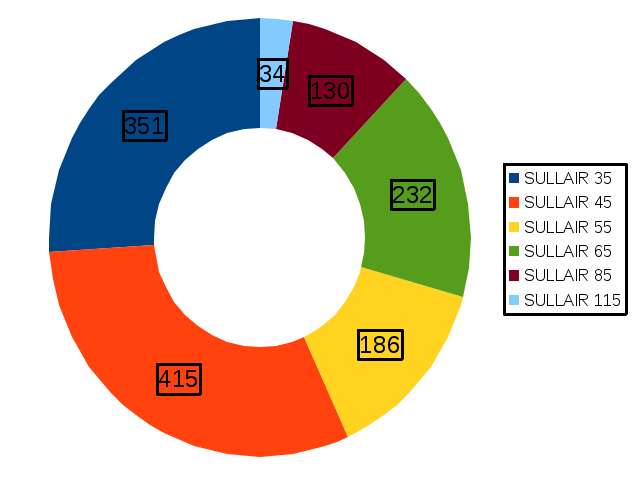
La ligne actuelle, dimensionnée pour 1500 compresseurs (répartis de façon homogène sur toute l'année) est saturée. Elle ne peut notamment pas faire face correctement à la demande lors d'un pic ponctuel de celle-ci. En effet SULLAIR EUROPE est le fournisseur de sociétés telles que KILOUTOU, MERA, COX...qui commandent occasionnellement de grands lots d'un type particulier de compresseur (S55 et S65). Ceci a pour effet de déséquilibrer la ligne et de créer des ruptures dans la chaîne d'approvisionnement.
Des réunions au sein de SULLAIR EUROPE ont définis les nouveaux objectifs à atteindre dans les années à venir pour faire face à la concurrence et assurer le développement de l'entreprise. L'objectif est de 2500 compresseurs par an.
À cette augmentation de production, s'ajoute une évolution de la série de compresseurs. En effet les modèles S35, S45, S55, S65, S85 seront intégrés dans une nouvelle gamme de compresseurs appelée SERIE 7. L'évolution de la série est prévue en 2 ans et commencera dès septembre 2003 par les modèles S35 et S45. Cependant, une amélioration temporaire visant à diminuer les coûts sera pratiquée dès que possible pour les 35 et 45.
Cette nouvelle série contiendra des améliorations technologiques (Bac de rétention d'huile, Caisse monobloc et capot allégé...) et des simplifications pour diminuer le coût du compresseur et le rendre plus compétitif (Radiateur double, élimination de certaines pièces inutiles...).
Enfin, un nouveau venu dans la gamme, le SULLAIR 115, le plus gros compresseur fabriqué à Montbrison a été mis en fabrication en avril 2002. Son intégration dans la ligne est à revoir étant donné sa taille.
Une réorganisation de la ligne s'impose en vue de concilier l'augmentation de la demande de compresseurs, la qualité du travail, l'intégration de la nouvelle gamme ainsi qu'une réduction des coûts de production.
Présentation de la ligne actuelle
La ligne actuelle se compose de 9 postes de travail sur lesquels travaillent 12 personnes en 2 équipes (2x8).
- MONTAGE DU CHÂSSIS :
-
Sur ce poste est réalisée la liaison entre la caisse en tôle et l'essieu correspondant au modèle choisi par le client. Il existe des essieux freinés ou non- freinés qui peuvent être montés avec des anneaux ou des attaches style caravanes.
- ACCOUPLEMENT :
-
Le moteur est assemblé avec le bloc vis, les supports et tous les accessoires nécessaires au fonctionnement et à la régulation du moteur.
- MONTAGE DES HOTTES ET DU RÉSERVOIR :
-
C'est sur ce poste que sont montés: la hotte de refoulement d'air et le réservoir. La hotte est équipée d'un radiateur et d'un filtre à huile, le réservoir de ses durites et du filtre à gazole
- MONTAGE DU SÉPARATEUR :
-
Le séparateur d'huile est équipé de tous ses accessoires (Soupape de sécurité, clapets anti-retour, supports et embouts divers,...).
- MISE EN GROUPE :
-
Sur ce poste est réalisée la liaison entre le bloc moteur, le châssis, le séparateur et les différents flexibles.
- MONTAGE DU TABLEAU DE BORD :
-
Le tableau de bord est assemblé avec ses différents voyants et interrupteurs.
- MONTAGE DU CAPOT :
-
Le capot est équipé de charnières, d'une grenouillère et de compas à gaz puis fixé sur le châssis du compresseur.
- POMPE :
-
C'est ici qu'est effectué le plein des différents fluides du compresseur:
-
Gazole
-
Huile moteur
-
Huile de compression
-
Eau
-
- SALLE DE TEST ET DE RODAGE :
-
Le compresseur tourne pendant plus d'une heure afin de roder le moteur et de vérifier l'étanchéité des différents raccords ainsi que les sécurités.
- FINITION :
-
Tous les travaux de finitions sont réalisés ici. On effectue tous les raccords de peintures, collage d'étiquettes et plaques d'immatriculations. C'est également le lieu des dernières vérifications des sécurités du compresseur (Grilles de protection...)
La ligne comporte également un petit établi de découpe de joints et de montage des câbles de batterie servant au poste de montage du châssis et à la mise en groupe.
En outre des magasiniers sont chargés du transport des pièces vers la ligne de production et de remplir les bacs vides.
- Taux d'occupation :
-
Nombre de personnes nécessaires à la réalisation des tâches attribuées.
Comme il s’agit d'une production en 2 x 8, les données du tableau concernent une seule équipe.
Sur chacun des postes de la ligne, des problèmes d'organisation sont constatés. Ce sont pour la plupart des problèmes de rangements inadaptés ou manquants (Outils rangés sur les étagères de stockages).
En voici quelques-uns:
-
Les joints caoutchoucs et les rouleaux de durites sont posés à même les étagères et occasionnent une gêne lors de leur manipulation.
-
Des box palettes sont stockés au milieu de la ligne et sont très difficiles d'accès avec les transpalettes. Leur déplacement vers les bords de la chaîne les rendrait plus accessibles.
-
La forme complexe de certaines pièces rendent leur stockage sur une étagère difficile. Les pièces s'accrochent entre elles, tombent, etc.
La meilleure solution est de les suspendre.
Déroulement du stage
Objectifs du stage
-
Mise en place d'une nouvelle ligne d'assemblage de compresseurs. La nouvelle ligne d'assemblage sera réorganisée en août 2003.
-
La ligne devra tenir compte de la nouvelle gamme de compresseur, intégrer le SULLAIR 115 et permettre la fabrication de 2500 compresseurs par an).
-
Les composants nécessaires devront être disposés sur chaque poste afin de réduire la zone de stockage.
-
Elle devra tenir compte de certaines installations indéplaçables comme la salle de rodage des compresseurs.
-
La nouvelle ligne devra également prendre en compte les règles de sécurité, une bonne ergonomie des postes de travail, etc....
Manquant dès le départ d'informations sur la SERIE 7, mon étude s'est plus appuyée sur la gamme actuelle des compresseurs (Notamment pour le rangement des pièces).
Classification des pièces
J'ai commencé par faire l'inventaire de toutes les pièces devant être utilisées sur chaque poste. Le travail suivant a été effectué:
-
J'ai listé toutes les pièces à l'aide des notices de montage sur poste (O.M.S.) et des inventaires mis à jour grâce à la base de données ACCESS de l'entreprise.
-
J'ai vérifié si le rangement de chaque lot de pièces était adapté à la valeur Kanban indiquée et changé ces rangements lorsque cela a été nécessaire.
-
Un classeur informatique a été créé, ordonnant les pièces par poste en indiquant leur rangement et leurs informations Kanban. (Voir exemple en annexe)
Le classeur ainsi créé permet de répertorier toutes les pièces pour chaque poste et de calculer le nombre de rangements nécessaires en fonction de leur encombrement et de la quantité sur poste. On peut alors calculer la quantité de pièces qui peuvent être contenues dans les stockages ou inversement, adapter les stockages pour maximiser le nombre de pièces sur poste.
-
J'ai ensuite effectué un tri entre les pièces indispensables sur le poste et les options.
Par exemple, le montage du châssis possède de nombreuses options de béquilles, d'anneaux et d'attaches très peu utilisées. Vu leur poids et leur encombrement, elles ne nécessitent pas d'être toutes sur le poste. Les pièces vouées à disparaître (Hottes, radiateur d'huile, etc..) sur les 35 et 45 SERIE 7 ont été signalées dans le classeur en fonction des informations dont je disposais.
Je suis parti du principe qu'il y aurait toujours à quelques exceptions près, le même nombre de pièces, les mêmes dimensions de châssis et d'essieux etc. La réorganisation de la ligne devra donc faire l'objet d'un ajustement en fonction des nouvelles solutions technologiques retenues.
Modification de la ligne en flux tendu (D.F.T.)
Définition des quantités à produire.
En me basant sur les ventes envisagées par la direction et sur leur répartition pour l'année 2002, j'ai calculé la quantité journalière de chaque compresseur à fabriquer.
MODÈLE | QUANTITÉ ANNUELLE À PRODUIRE (2005) | QUANTITÉ QUOTIDIENNE À PRODUIRE |
---|---|---|
S35 | 650 | 3.00 |
S45 | 765 | 3.53 |
S55 | 350 | 1.61 |
S65 | 425 | 1.96 |
S85 | 250 | 1.15 |
S115 | 60 | 0.28 |
TOTAL | 2500 | 11.52 |
Calcul des boucles Kanban
-
Avec la base de données ACCESS j'ai redimensionné les nombres de Kanban pour pouvoir satisfaire les objectifs de vente. Pour cela, je me suis basé sur les ventes de compresseurs pour l'année 2002 fourni par le service commercial.
Ces valeurs seront intégralement valables pour les modèles S55, S65, S85 et S115 car ils ne subiront pas de modifications d'ici septembre 2003.
En revanche, les valeurs données pour les S35 et S45 ne sont valables qu'en partie étant donné les modifications importantes que vont subir ces modèles.
-
Pour pouvoir réagir rapidement à une demande brusque des compresseurs de type S35 ou S55, il m'a été demandé d'ajouter à la base de donnée les valeurs Kanban données par une consommation quotidienne exclusivement composée d'un de ces modèles.
Ceci permettra de modifier rapidement le nombre de cartes et de passer des commandes en prévision d'une forte demande de ces compresseurs.
Cette modification se fera d'autant plus rapidement que le passage à une gestion informatique des Kanbans est prévue.
Modification des paramètres D.F.T.
Définition de la séquence des évènements.
-
Pour redimensionner correctement la ligne, j'ai procédé avec monsieur Henri LEFEBVRE à une analyse de déroulement. Cela consiste à observer chaque étape du montage et à noter le temps que prend chaque opération.
Toutes les actions sont chronométrées ainsi que les déplacements et les contrôles réalisés par le monteur. Cette analyse permet d'avoir la séquence des évènements et des temps de montage précis.
On peut ensuite déterminer les problèmes liés aux déplacements excessifs, aux solutions de montage inappropriées et à l'organisation de la ligne (Voir extraits en annexes).
L'analyse n'a été faite que pour les modèles 35 et 45 par manque de temps. D'autres mesures moins précises ont toutefois été refaites sur les autres modèles pour contrôler les valeurs existantes.
Les résultats trouvés sont à certains moments très différents de ceux notés sur l'ancienne feuille de calcul DFT, des simplifications ayant déjà été faites sans avoir été mises à jour.
-
Après cette analyse de déroulement, j'ai fait des estimations sur le temps que les nouvelles solutions technologiques permettront de gagner une fois mises en œuvre:
-
Le nouveau châssis devrait se monter plus vite et diminuer le temps de retouches de peinture. Sa forme permettra de se passer de la hotte de refoulement d'air, de divers supports et d'éviter le montage de pièces inutiles.
-
Des gains de temps seront aussi réalisés au niveau de l'accouplement et du montage des hottes. En effet la SERIE 7 n'aura plus qu'un seul radiateur combiné et plus de hottes du tout.
-
-
Au début du mois de décembre, une nouvelle information m'est parvenu concernant certains éléments des compresseurs.
Si la décision est prise définitivement par le service achat, le séparateur pourrait arriver déjà équipé dans l'atelier.
De même, le tableau de bord serait livré directement sur le châssis et ne serait plus monté dans l'atelier. Ceci impliquerait la disparition pure et simple de ces deux poste et une redistribution des tâches à l'intérieur de la ligne.
Pour le reste de mon étude, j'ai considéré que l'assemblage de ces deux composants n'était plus réalisé sur la ligne (La confirmation ne viendra qu'au mois de janvier voir plus tard).
Voici un récapitulatif des temps trouvés et des temps estimés pour tous les compresseurs:
Notes:
-
Les temps donnés sont en minutes.
-
Le temps de rodage homme est le temps que passe l'opérateur à régler chaque compresseur durant son fonctionnement et non le temps de rodage du compresseur lui-même (Temps de rodage machine).
-
Le temps de cycle est le temps que met un compresseur à être fabriqué. Il est déterminé en remontant la ligne de la fin par l'arborescence de process la plus longue.
Calculs.
L'ancienne feuille de calcul de la ligne DFT a été modifiée. J'ai remis à jours les temps de montage et changé certains paramètres obsolètes (Montage des feux, de certaines options,etc.) pour pouvoir redimensionner la ligne. (voir explications des calculs en annexes)
Affectation des ressources.
Voici un extrait des résultats obtenus:
En analysant les résultats, on constate plusieurs choses:
-
La nouvelle ligne comptera 8 personnes par équipes (16 au total), soit 2 de plus qu'actuellement.
-
Le poste accouplement sera double afin de fournir suffisamment de moteurs sans ralentir la ligne.
-
Les opérations effectuées sur la mise en groupe doivent être partagées. Un nouveau poste doit être créé sur lequel seront réalisés la pose du réservoir ainsi que le câblage des tuyaux pneumatiques du circuit de régulation.
Implantation de la nouvelle ligne
Après avoir défini tous les paramètres concernant la ligne DFT, j'ai pu commencer à établir, avec les suggestions des ouvriers et de monsieur Jean-Claude RONDEL, une première implantation de la ligne.
L'idée de base pour cette nouvelle ligne est de supprimer en partie les étagères de stockage et de faire une ligne. De plus le montage du capot serait ramené avant le rodage, ce qui est sa place logique dans la séquence de montage d'un compresseur.
Cette première implantation a été présentée début décembre aux 2 équipes de montage afin de connaître leur avis à ce sujet:
-
La forme générale de la ligne a été bien acceptée à part certains détails comme la trop grande distance entre le poste de montage du châssis et le poste accouplement.
-
D'autres suggestions m'ont été faites:
-
Déplacer la pompe contre la salle de rodage, supprimer le couloir d'accès (Inutile si le montage du capot est avant le rodage) et gagner de la place.
-
Augmenter la surface de montage du capot.
-
Aligner la mise en groupe, le montage de la régulation, le montage du capot et la pompe afin d'éviter de tourner les compresseurs.
-
En consultant monsieur Bernard GIBERT, responsable hygiène sécurité et environnement, j'ai appris qu'il n'existe pas de distance réglementaire à respecter entre le gazole et la salle de rodage. Le déplacement de la pompe est donc possible.
Pour éviter certains problèmes que connaît actuellement la ligne, d'autres contraintes doivent être prises en compte:
-
Pour faciliter le travail des transpalettes, les palettes encombrantes doivent être ramenées sur les bords de la chaîne de montage.
-
Les palettes dont le contenant le permettra seront empilées sur 2 étages pour les grandes et sur 3 pour les petites. Ceci permettra de stocker plus de pièces sur le poste en toute sécurité et en gardant une bonne ergonomie.
-
Tous les godets en plastique seront sur des stockages dynamiques (Étagères inclinées avec mise en file).
-
Des rangements spéciaux seront créés pour pouvoir accrocher les flexibles et descentes d'échappement dont la forme le permettent. Ces rangements serviront aussi de support pour le stockage des rouleaux de durites et de câbles.
-
Des rangements pour les outils seront mis en place pour éviter la pose de ceux-ci sur les étagères de stockage comme c'est le cas très souvent.
-
Les problèmes de disposition propres à chaque poste devront être pris en compte pour améliorer l'ergonomie et le travail.
Une deuxième implantation de la ligne à l'échelle a été faite pour positionner exactement tous les stockages et postes. Voici un schéma simplifié de cette implantation:
(Pour le plan complet voir annexes)
Cette nouvelle implantation de la ligne permettra de:
-
Limiter les déplacements inutile des compresseurs.
-
Gagner de la place
-
Gagner en productivité
Estimation des coûts
La réorganisation de la ligne nécessitera les investissements et opérations suivantes:
Déplacement du palan portique de 1000 Kg pour le poste accouplement. | 3000€ |
Déplacement des autres palans. | 5000€ |
Peinture du sol, pour une surface de 590 m2 environ. | 18000€ |
Fabrication de 13 stockages dynamiques et de 2 portes flexibles. | 6000€ |
Achat d'un nouvel établi pour le montage du faisceau. | / |
Achat d'une nouvelle table élévatrice pour le poste régulation. | 3100€ |
TOTAL | 35100€ |
Avenir du projet
Pendant toute la durée de mon stage, j'ai été confronté à beaucoup d'incertitudes concernant la SERIE 7. J'ai donc dû commencer mon étude en m'appuyant essentiellement sur la série actuelle en supposant que, hormis certaines différences technologiques, les nouveaux compresseurs auraient beaucoup de ressemblances avec les anciens.
La réunion de présentation du projet à la direction de SULLAIR EUROPE le 17 janvier 2003 sera une étape décisive pour connaître la validité et l'avenir de la réimplantation de la ligne.
Pour que mon projet soit correct, il faudrait aussi valider certaines hypothèses que j'ai posé pour pouvoir avancer:
-
La solution technologique concernant le châssis monobloc est elle bien celle que souhaitait retenir le service des achats?
-
Est-ce que cette solution technologique implique de nouvelles opérations à réaliser sur la ligne?
-
Les fonctions qui devaient être intégrées au départ permettent-elles les gains de temps de montage prévus?
-
Le montage du séparateur et du tableau de bord est il définitivement abandonné pour la ligne?
Certaines de ces questions ne pourront avoir de réponses certaines avant mars-avril 2003.
Mon étude devra donc être reprise par une personne de l'entreprise ou un autre stagiaire afin de:
-
Vérifier les temps de montage.
-
Mettre à jour les paramètres de la ligne DFT qui auront changé d'ici là.
-
Mettre à jour la liste des pièces sur postes et leurs valeurs Kanban.
-
Prendre en compte les nouvelles contraintes posées par la SERIE 7.
-
Réaliser les cahiers des charges définissant les travaux à réaliser (Pour les entreprises extérieures).
-
Rédiger les demandes d'investissements nécessaires.
-
Contacter les entreprises concernées.
Conclusion
Le premier stage en entreprise est un passage difficile dans la vie d'un élève ingénieur. Celui-ci doit s'impliquer rapidement dans une entreprise, un projet et une vie qu'il ne connaît pas et acquérir des connaissances pour son futur travail.
Ce stage m'a beaucoup appris sur la façon de mener à bien un projet depuis son ébauche jusqu'à sa réalisation finale. J'ai appris à communiquer constamment avec les différents services pour obtenir rapidement les informations nécessaires et avoir de nouvelles idées, mais aussi à informer les autres de ce que je faisais pour faire gagner du temps à toute l'équipe.
Le contact avec les différentes personnes qui ont travaillé avec moi m'a permis d'acquérir des connaissances, notamment sur la gestion des stocks, l'organisation en flux tendu, ou encore sur l'estimation des coûts.
Je tiens encore une fois à remercier monsieur Jean-Claude RONDEL pour m'avoir fait confiance tout au long de ce stage ainsi que l'ensemble du personnel de SULLAIR EUROPE pour m'avoir accueilli.